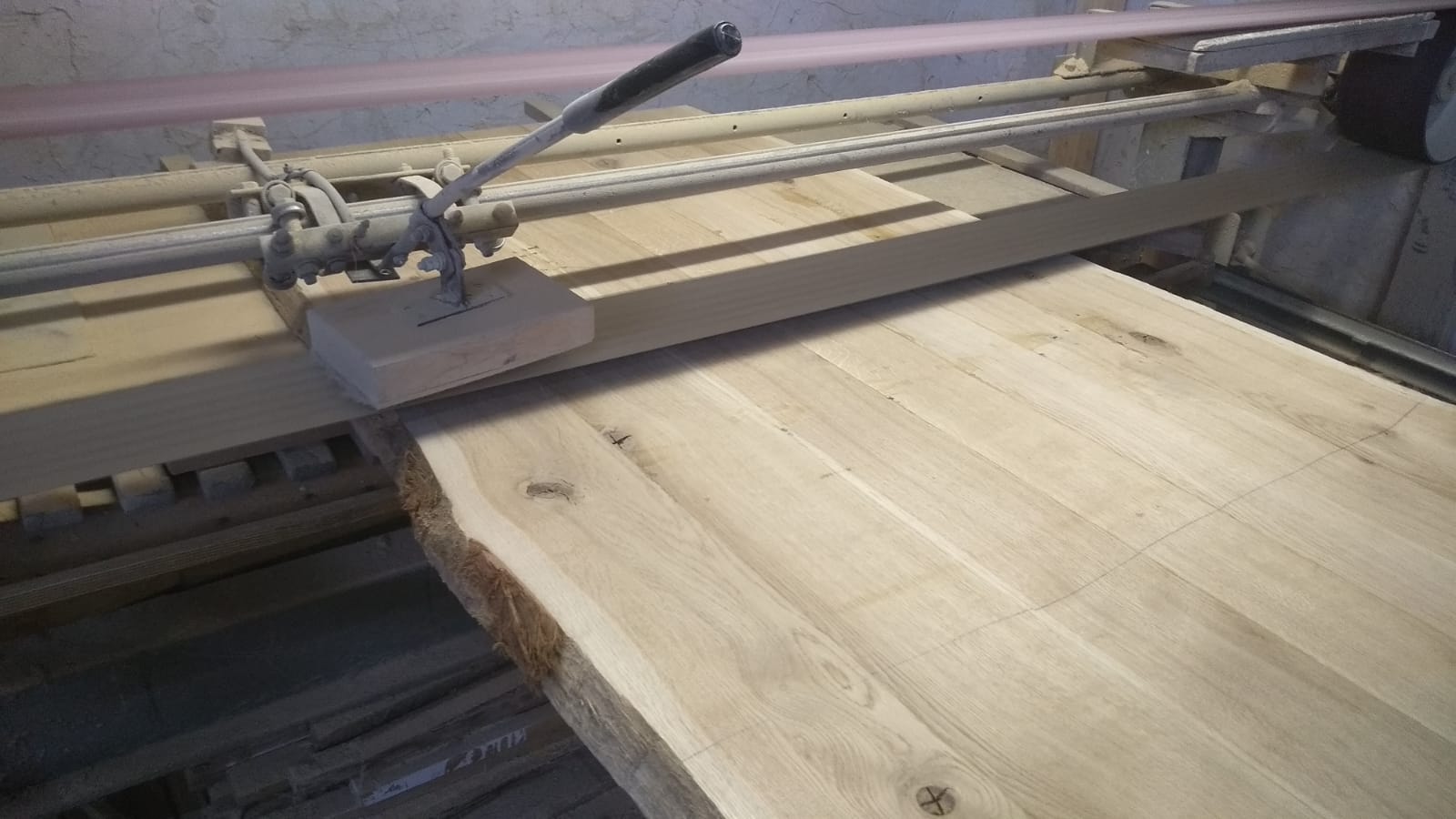
Assembling a rustic industrial table
This is one of my favourite projects. Using 100% recovered wooden planks I generated a rustic industrial table. It took some time to prepare the timber and finish a perfectly smooth end, but the final result is totally amazing.
The timber came from a buddy’s lost old decking.
After the timber was initially offered to me personally I was not sure on account of this illness, but I chose to move ahead and see what I could make out of it. I am happy I did!
Engineered wood can be tricky to use, but it is absolutely worth it to save several trees and understanding that you can turn something very horrible to a gorgeous piece of furniture.
1. I started by removing all of the nails and screws.
This was a challenging job and that I needed to purchase a larger crowbar/canning pub to aid with the rusted nails. A few of the claws snapped within the timber so that I needed to knock them with a nail punch.
2. The following job was to sand and plane every individual slice.
After planed, I cut every slice using a belt sander and an orbital sander to make a great smooth finish. This was significant since the next step is to glue the pieces together and the smoother the timber the greater the contact between 2 bits.
3. Fixing all of the bits together was up.
This system cuts an even groove to the face of the timber in which you may put an as little slice of wood (known as a biscuit) to make sure two-part lineup against each other. Some say that it also adds a little bit of power to the combine but it’s largely for making sure a perfect orientation.
After all of the pieces were trimmed with all the biscuit jointer it was time to get a few glueing. Clamping some beams around the top and underside here in order to guarantee an entirely flat end whilst glueing.
4. Glueing.
I bought some extra knobs for this particular part. I had to achieve across the diameter of this table that was approximately 90cm.
To guarantee the table didn’t bow after tightening the straps I used a few thick pieces of wood to brace across the top and bottom and firmly clamped each down one in either end.
I have done all the glueing onto a flat surface to make sure the entire piece was perfectly horizontal. Any bowing from the timber or joins could have been quite awful and made a table.
You’re going to want some good wood adhesive for this particular part. The adhesive dries fairly fast but I made it to be certain.
The following task was to cut on each end and then paste the pieces on at precisely the exact same manner as previously. I utilized ratchet straps for this particular part.
I then followed up with sanding to find the table as easy as possible before I began to fill any imperfections and gaps.
The table was ready for incorporating a few epoxy resins to provide the table with a totally smooth finish. You do not need to use sandpaper with this and also an easy wood filler may give a great smooth finish into the table.
Bear in mind, the timber was in rather a bad way when I started cutting on it had plenty of pockets and imperfections. The strategy was supposed to tape off the areas to match with resin, blend and put in one go because you just get a few hours prior to resin begins to place.
I began using some fundamental electrical tape to cover all of the joins and openings on the bottom of the table. This would avoid any dryer leaking through the floor.
I then blended the resin in a little cup and started to pour. This was catchy and I found myself arriving a lot of places because the resin leaked deep into the timber openings.
I allow the resin place overnight. It was essential to guarantee the temperature was approximately 18 degrees Celsius from the workshop to be sure the resin did not cloud over.
com. Whether you are constructing a new dining table, creating some jewellery or producing a piece of artwork, this is a superb resource for all matters sandpaper.
Once installed, I started to manually air spray the entire surface, followed by heaps of sanding. For those components with resin, I moved all the way around some 1200 grit paper to provide the resin with a super clean conclusion.
Not my work but a local welder pulled them for me. I desired a thick chunky leg went to get a 70mm box steel using a 100mm top runner for attaching into the table.
Many tables similar to this have a metal bar from 1 side to another however these legs were strong and did not require any extra support.
The entire table was finished off with a couple of coats of Osmo Oil and gently sanded after each coating.
1 hot industrial table. Enjoy it!
Construct your personal or purchase one of mine.