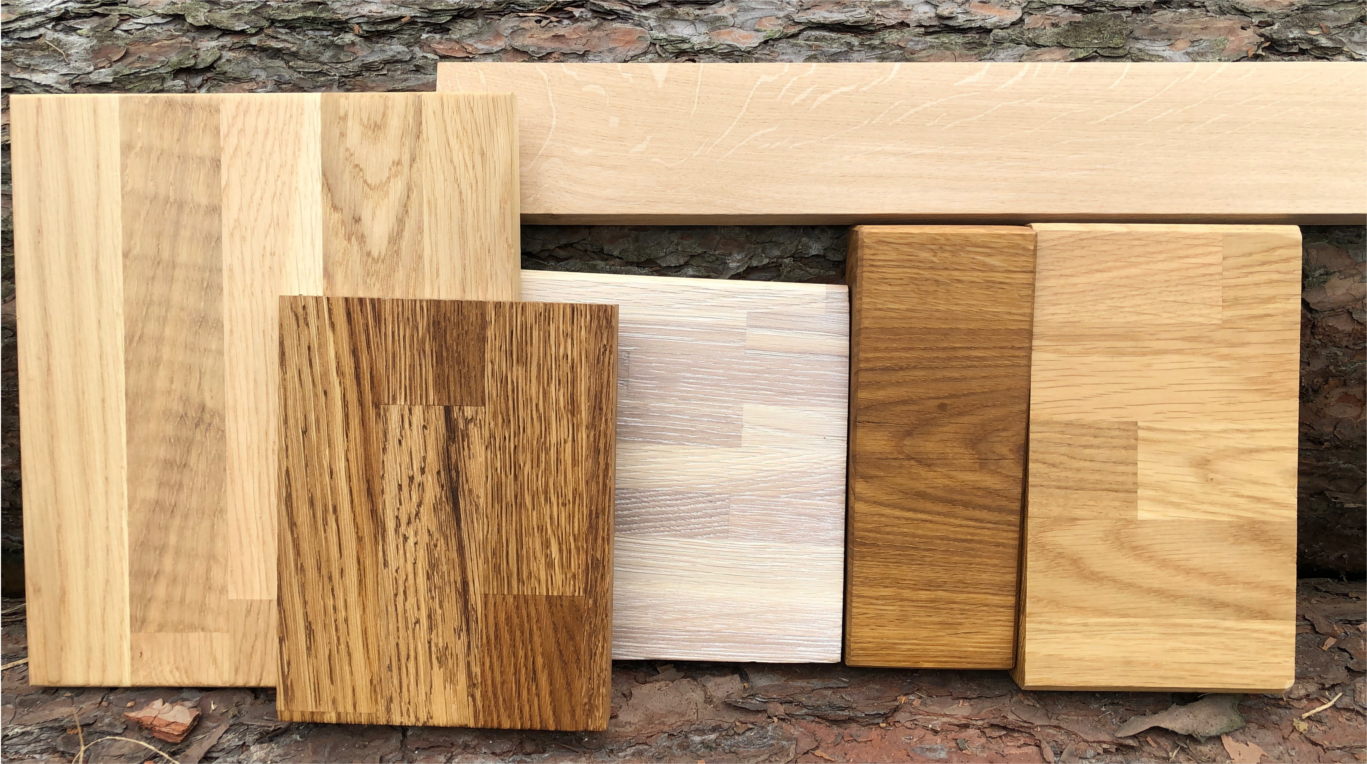
Solid wood versus glued laminated wood – what are the differences between them and what does it really mean.
The text below was created in order to describe, in a broad and accessible way as possible for an ordinary “furniture buyer”, existing divisions of furniture on the domestic market in terms of the natural 100% wood from which they are made and doubts that have arisen over the years related to the terms used in sales and on websites.
These doubts have arisen partly as a result of creative “marketing” and the speech of benefits used in advertisements and a certain blurring of meanings as a result of a decrease in the domestic market share of small, several-person carpenter companies in favour of larger, multi-series production companies.
At the outset, we would like to draw your attention to the frequent practice of small and large manufacturers to describe furniture as wooden in the title and only in the product description or its characteristics to add that the wooden element is only the front. That is the number one rule when buying furniture: read the description and characteristics in small print. Otherwise, our dream ‘wooden’ furniture may turn out to be made of 75% melamine board or veneer, which is discussed below.
Veneered furniture, due to its appearance, also often has the word “wooden” in its name. And this is true, but not complete. A veneer is a thin slice of natural (0.5mm to 1.8mm thick, sometimes a little more) veneer. A patch of wood is created by machine slicing a felled trunk. Such a cover retains some of the properties of wood but is much cheaper than full 100% wood. You can say that it is lighter on the wallet and the appearance and aesthetics at a similar level.
Sometimes even this “aesthetics” is an interesting solution. Because veneer is often carefully selected, purchasing veneered furniture (pictures below from our model bed veneer oak Alvis) we can get rid of the disadvantages (or advantages depends on the user’s view) such as knots or heartwood.
The keyword that influences the whole process of furniture making is the raw material – TREE. When you buy a wooden wardrobe or a wooden chest of drawers, you expect it to be made entirely (or to a very large extent) of wood. Let us assume that the back of a wardrobe and a chest of drawers, as well as the bottom of drawers in a chest of drawers, will be made of plywood. This does not increase the price of the furniture and is commonly used by manufacturers and “accepted” by buyers.
So why do some people turn their noses up when a seller says that a piece of furniture is made of plywood? And why is it possible to meet voices that: “solid wood is great and plywood is blah”?
Simply put, the word LITE WOOD has changed its meaning over the years.
At the moment, based on our long experience, observation of the market and thousands of conversations with customers, we can be 80% sure that when we talk to a person who wants to buy furniture and not goes into details, when we hear: solid wood our interlocutor means, for example, a bed made of wood where no wood-based materials were used.
That is, when someone asks about a pine bunk bed, he or she is not interested in how the pine elements are cut or how they are joined, but whether the piece of furniture is made of wood with specific parameters and material that before it became wood was a slow-growing tree (one that drew minerals from the soil and for n-teen years was under the open sky, rain and sun).
The remaining 20% are those who mean solid wood in the sense of glulam joined (lamellae) lengthwise, but more about that below.
What is glulam?
And what is this “DEMONIC glulam”? The tree is felled and goes to the sawmill under the saw. And this is where it comes in: glulam.
Information about the strengths of glulam is included at the very bottom of this material.
Glued laminated timber is a child of the industry, technology and a change in approach to production from single pieces polished by a carpenter’s hand and a tool to a large-scale machine processing. Now the precision of production is not controlled by an experienced eye and hand of a person who has been learning for many years, but by a tireless and insensitive to mechanical fatigue tool of a fully automated CNC machine. And here not one bed is made every day, but tens and hundreds. Only automated production lines are able to ensure adequate accuracy, precision and repeatability.
Plywood is a type of furniture board (the name board refers to the creation of the surface of the furniture such as sides/walls) created from glueing together several pieces of cut wood. The term solid wood among carpenters (but not e.g. sellers in shops and showrooms in Poland) refers today to glulam joined lengthwise, i.e. planks from a trunk cut to length and joining the longer sides of the planks to form a piece with a larger width than the original trunk. If the trunk is not big enough, it is made by joining narrower boards together. Such a trick.
And it’s a good thing, too, because otherwise, the entire timber industry would have died a long time ago, waiting for trees that are big enough (and thick enough in circumference) to grow. I’m not even going to mention such detail as transporting such a colossus or even moving it from the felling site in difficult terrain.
If you have the time and inclination, we invite you to our showroom, about 15 minutes from Manchester, to take a look.
A board cut from a log to length. According to the old usage of the word “solid,” it should be the best element for furniture production. Provided that we have at hand, as I mentioned earlier, trees with the appropriate girth size. The common pine does not reach monstrous dimensions in the country (taking into account the species structure of forests, we have about 60% of them and for comparison about 8% of oaks). Therefore, pine is often used as logs, i.e. bedsides connecting the bottom and the top of the bed (headrest). In use, exceptionally large trunk pieces are called MONOLITES. And they are mainly used to make beautiful tables with an uneven edge (that side of the lumber which is the side surface of the trunk after cutting it lengthwise).
What is currently used as “the most desirable solid wood in the marketing sense” is… glulam joined at the length of the lamellae. In addition, this wood has all the blemishes of wood, so it is called “wild oak”.
Another way of joining the lamellas is the so-called ‘microglulam’. That is, elements cut from the trunk in width and length.
Strengths of glulam and solid wood
Glulam is stronger than a board made of a single piece of wood. It does not warp or bend. It does not crack under stress. Its resistance is manifested, among others, by the fact that it does not creak even after prolonged use. If properly protected, it can cope with increased humidity or liquids. In this case, hard oils are used to impregnate surfaces such as countertops.
A little known feature of glulam in glulam/micro strand technology is increased resistance to burning. In practice, fire chars the top layer of material creating a “temporary” barrier.